"Hi Nate. As my years of bow making progressed, I did make some subtle changes. I also observed things that Mr. Hill omitted, which I blended into my bows, yet staying with his basic design. His own bows will show similar, what I call refinement, from the 1930s-40s. I believe those were his best bows, during those later years.
Regarding a certain longbow, he wrote me saying if I could build it, he would "take a back seat to you as a bowyer". He later commented it was the most near perfect bow he'd ever seen anyone make."
The above quotes were from texts that John Schulz sent to me when I mentioned certain particulars that I'd noticed in his bows over the years. I have a few of John's bows, from different eras and although he made changes to accommodate the wishes of his employers at times, and he incorporated certain design features to work around the qualities of the materials he had available, he always held to Hill's basic design. This photo shows two of John's bows while building bows for Ted Ekin of Howard Hill Archery. Both bows are made with no tip inserts...the earlier bow which has black glass has very small tips and a very skinny handle. It came to my possession through a friend, from the widow of Ed Hill, a friend of Howard's that accompanied him to Africa and is the fella fighting the python in "Tembo". Ed happened to retire to and pass away while living in my home town. Anyway, I showed this bow to Schulz and asked about the tiny tips and skinny handle sweeps. He said that bow was built for Ted under Ted's direction that the bows made by John had to look like the bows built by Don Burdette who had ceased building bows for HHA. Ted didn't want the public to know there'd been a bowyer change. Don built bows in this manner, so John copied them. The second bow has a brown back and white belly and even though it's a couple hundred bows later down the line, it has some of same characteristics in the handle although the tips were starting to get a little wider. I discussed with Schulz that he made wider tips over the years, departing from the real narrow ones of his early bows. He said with a smile, "the wider tips are a little more stable, less prone to twisting...and even an old dog can learn new things if he does them long enough" This statement falls in line with the limb twisting encountered as bamboo quality gradually got worse.
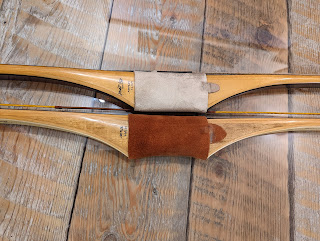



One thing to remember, that these bows built by the Hill bowyers over the years, including Schulz, were being made for the public in great quantities. The techniques used by the bowyers had to be streamlined and of quality that would hold up in the field. No one wanted warranty issues caused by limbs or handles twisting, or bamboo belly chrysalling or things like that. The bowmaking techniques Hill preferred to get his concave convex limb design were hard to use when making lots of bows, due to the length of time the process took. Using fiberglass on flat limbs greatly improved the success rate but until Schulz had an epiphany of sorts, all the bows were still being made in the two stage process.
The two stage process was done by building the stave including the handle, shaping and tillering the stave and then adding the backing or fiberglass. Hill determined that this was the best way to build his style of longbow. When Schulz had obtained a few years of bowmaking under his belt, he had a meeting with Tom Jennings and Tom discussed the bowmaking method of building the bow in all one step...meaning the entire bow was glued up at one time then shaped and final tillered. John went to Hill with this idea...it wasn't new, just new to John because Hill had taught him the Hill way and that's the way that John built all his bows. Hill said it would not work to tiller the bow after the glass was applied, all in one build.
John thought the process through and kept track of the dimensions of his limbs after he'd tillered them and before he added the glass. After some time he had a good idea of what the proper limb taper was to get the proper Hill limb tiller profile. John made some jigs and pre-tapered his limb lams to the proper dimensions. This Hill style limb taper is NOT a straight taper from handle to tip, fyi. It is a varying, graduated taper. John built a bow using his pre-tapered lams, finished it with glass and took it over for Hill to inspect. Hill did so and commented on what a good bow it was. Then John spilled the beans and said the bow was not made in the Hill fashion of shaping and tillering the limbs as a stave before adding glass...but rather the process had all been done in one step because the lams were pre-tillered before glue up. Hill could hardly believe it and John said he asked to inspect the bow once more. After doing so, Hill proclaimed that "I guess the old man was wrong". John said at that point, Hill gave him the approval to build all the Hill style bows in that manner and from then on, that's the way that Schulz built the Hill style longbow, for Shawnee Archery, Howard Hill Archery, and American Longbow. Here again is the refinement of the Hill style longbow coming into play over the years.
What was very important to Hill and Schulz was the limb tiller. Schulz called it the Gothic Arch. If you look at his bow limbs throughout the years and thousands of bows, you'll see what I mean. The limb did not have excessive limb bend at any point from handle to tip. There is no variance to the parabolic shape (Gothic Arch) of the limb. You can see this limb shape in the next photo. The Gothic Arch in action...The same two Schulz-made bows as pictured above, with two of my bows laying on top. They mirror. I do not know the exact formula that Schulz used to pre-taper his limbs...he never divulged that to me. However, I build bows in a similar manner to the original Hill method because I don't build them for a living and need the quantity. I tiller the limbs and add the glass. I come up with the same tiller as Schulz through a different process. This was approved by Schulz when he inspected my bows, and the important thing to him was that the tiller aka braced limb profile shape was the correct Gothic Arch. John liked to say that he could pretty much tell how a bow shot by looking at it's braced profile.

I encourage all to brace your bows and see how close they come to the Hill-preferred and Schulz-promoted Gothic Arch, the limbs bending all the way down "into" the handle, with no straight section of non-working limb extending from the handle. As Hill said, each inch of limb has to do it's share of the work. Subjects for another time. Until then,
It's too bad Schulz didn't share the particulars of his design before he died. But I bet he kept notes. If his son's have decided not to follow in his footsteps, I wonder if they would share those notes with you and the larger archery community. Ultimately, knowledge should be shared (that's why patents and copyrights expire). I think it would be an invaluable addition to the archery world to have those notes published. Another project to fit into your busy schedule?
ReplyDeleteSteve, my sentiment as well but some of the process is moving painfully slow
DeleteYour last few writings about the history of John, Howard, the materials and methods have been very enlightening. Hopefully somewhere there's a few historical disussions to share about handle size and shape in our future readings.
ReplyDeleteJohn Schulz taught bow building one on one to several men, Pete George, David Miller and others.
DeleteThat is correct. He taught the art of the bamboo backed bow to Miller, the art of the glassed bow to Pete George. Pete built a few bamboo backed bows and Miller has built glass bows based on their study of Schulz's models, as I have done. Schulz also taught Jean-Marie Coche of France the glassed bow and Jean-Marie passed the information to Donato Milesi who has built glassed bows for many years. Schulz also taught his sons and as far as I know, only Dave is building bows occasionally and they've got some glass in their makeup. Besides that, Schulz's students still living or practicing are very few.
DeleteGreat read with a lot of info from John.
DeleteThanks Nate
Very Good Nate..I learn something new every time.
ReplyDeleteThanks Nate
ReplyDeleteyou had shared that gothic arch with me before and I keep thinking about it
also you mentioned something about refinement in final shaping- hopefully you will elaborate on that in another post
Awesome read!
ReplyDeleteGreat read Nate.
ReplyDeleteI can see how Schulz would want to eliminate steps in the production process to produce bows on a commercial "need for speed" basis. It is also good to note that he did this while remaining faithful to the original design concept and quality, something sadly lacking in todays world.
Having said that, did he ever express a view on whether he preferred one process over the other outwith the production environment?
In regards to the question, John only discussed the simplicity of building bows in the latter method compared to the complexity of the original Hill method. Obviously it is a simpler method of you already have the variable limb tapers figured out and can glue up the bow all at once. The several Schulz bows I have and have worked on show varied amounts of limb trapping so he did adjust limb weight and taper to some degree to allow for the inconsistency of glass and bamboo, but all in all it's a quicker way of getting a bow out the door when there are mouths to feed.
Deleteis that why Jack Howard spined his laminations and glass to match before gluing up (kinda combining the 2 techniques )?? and would glueing again (gass) after the initial glue up, affect the bonding of the initial glue going back in the hot box after cured?
DeleteMany bowyers spine their laminations, both wood and glass to keep some consistency. I imagine that's what Jack's premise was.
ReplyDeleteOne of the great things about Smooth-on epoxy is that you can cure it at different ratios to be strong in different applications. Many people don't read the directions on the can and utilize those benefits in the different stages of building bows because for the vast majority of bow builders, they all build the same, in one glue-up setting.
Thanks for answering
DeleteNever built a bow so a lot of unknown stuff to me
I am loving this. This information is so enlightening. Thank you Nate for keeping it alive. Look foward to more
ReplyDeleteIt is very interesting that you use Howard's original construction process in the building of your ASL's. Having never shot one made this way has me curious as to any differences in feel or performance.
ReplyDeleteI use a few of the original techniques so I can tiller the stave before adding the glass to lock in the tiller. Using a straight limb taper that comes from pretapered lams doesn't quite do it. There is a difference in feel and performance, but that can be subjective because a lot of people want an ASL to feel or shoot like their other bows, and they modify it to do such, ... And they can't feel the nuances.
ReplyDeleteThanks for the explanation Nate. There is nothing that feels or shoots like an ASL, which I'm certain is the largest single reason folks like us are so passionate about shooting them in the way they were meant to be shot. The history just rounds out enjoyment of the package.
DeleteGreat Article. As the world has fewer and fewer people that know the methods Hill then Schulz used to build their bows I think there is growing need for someone to write a book or a series of articles to preserve the information before it is lost forever. Thank you for the interesting article.
ReplyDeleteI have been a follower of HIll and Schultz since I took up the longbow in the early 80's. Dallied with other bows to most notable Bighorn longbows from the time Asbell started BH bow company. I was luck enough to test the designs etc. he would send back to a fella that ran a trad shop in Bloomfield NY. But I digress, as for the Hill side and Schultz side of things I've owned or shot so many different makers of the Hill/Schultz style I can't remember them all. Probably the BEST Schultz I ever shot was a Trophy hunter at the first Muzzy invitational. A fella had an old Trophy Hunter with woven glass on the back and no backing on the belly. It was a heavy bow to be sure but I shot very heavy ASL's back then when younger anyways. That bow was like butter to draw even as heavy as it was. Later as in years later I had Craig make one similar in style in the Big5 model at 70lbs but quit hunting for years and like a dope sold it. I owned Mountain Man yew bows, Strunk bows and one I still own, Templin bows, Kramers, Cole, Ekin's(a lot of those), a guy from Conn. that made wonderfull ALS's if you asked him!,(Gus DellaGellfa), Hamilton, and maybe the BEST of them all as far as I am concerned Pete George. Some others too, and the one that slips my mind I had an all osage bow of his that was great.
ReplyDeleteI always thought that Schultz used a running taper to his glass backed bows using I think what was the rule of thirds or something like that. For every foot of limb the limb lam tapered 1/3rd the thickness of the limb. I could be wrong but I am sure it was something like that. Anyways I owned several TH's over the yrs but none were better than the one I shot at the first Muzzy shoot. stay safe and keepem sharp
This comment has been removed by a blog administrator.
ReplyDeleteLongbow here, I should clarify a couple of comments here on my all wood string follow lemonwood bows and a couple of others. The all osage bow mentioned above was made by Dave Miller. They lemonwood bows are only backed with glass, solid wood, no multi lams, lite weight bow has a very short riser section built up and the heavier has a slightly longer riser section built up but both bows riser section fade very nicely into the belly not abruptly cut off as in squared off. It is interesting to note that with both strung the limb arc is nearly identical to both. Now the the Styx I have that was made By Tom Cole out of Penn. has a long riser of near 15" as near as I can measure. It's brown glass and a dark brown almost reddish brown colored core lams(3) that might be imbuya I don't think osage or yew wood although it might be yew wood. Point being is that it's made in what I call the classic early Hill design with the rounded bumper type lambs rounded on the sides back to front and front to back. It draws a bit more than my lite weight draw lemon wood bow but less than the heavier lemon wood bow but is stiffer to draw than the heavier lemon wood bow. Just not as smooth but seems to have decent cast though. Bulbous handle and not slim or peaked like on my Templin bow or the lemonwood bows. The grip is thick through its center. Comfortable though and far from center shot. I may modify the grip a bit this winter as the spirit moves me and put a bit of a trough on the shelf. stay safe and keepem sharp
ReplyDelete